High-speed pumps master complex PUR applications
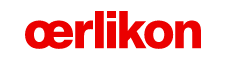
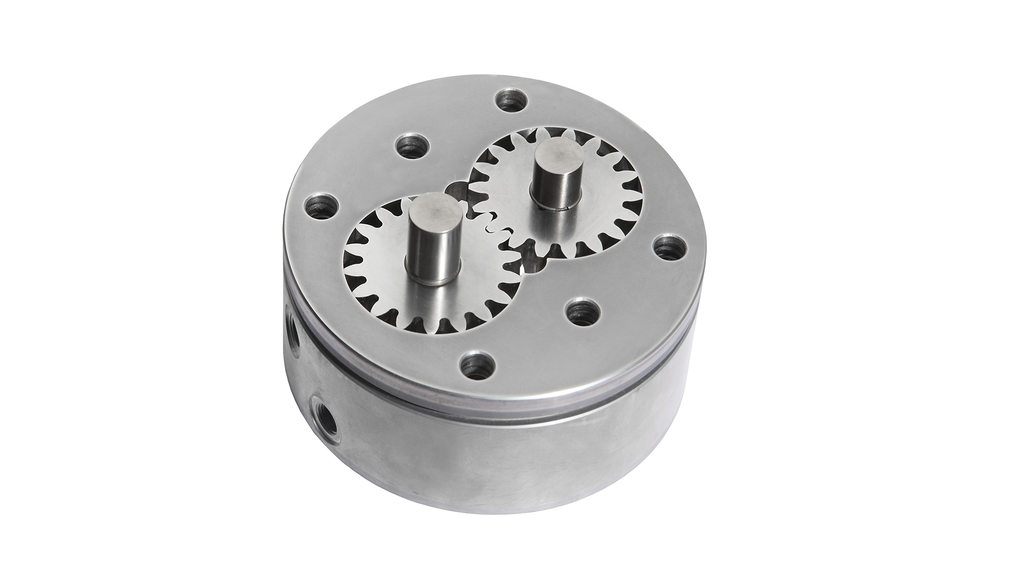
The range of metering pumps for chemical applications is available for conveying volumes of between 0.05 and 200 cm³/rev. Furthermore, it is characterized by its short flow channels.
Remscheid, July 1, 2021 – whether in the construction industry or in automobile building, in sports and leisure or in manufacturing furniture, for insulating or for sound-proofing, polyurethane has become an integral part of our everyday lives. Its applications are as diverse as the respective manufacturing processes are complex. With tailor-made solutions even for the most demanding tasks in the chemicals industry, increased productivity and durability, the precision metering pumps that Oerlikon Barmag will be exhibiting at this year’s PU China – taking place in Shanghai (Stand 225) between July 28 and 30, 2021 – are truly impressive.
Pumps for all purposes
Oerlikon Barmag pumps reliably master demanding processes in PUR applications in the chemicals, plastics, paints and lacquers industries. One of the biggest challenges is metering poorly-lubricating media. With the GM and GA ranges and the corresponding components, Oerlikon Barmag supplies the optimum equipment for the relevant applications. The high-speed pump in particular fulfills the expectations of the chemical industry with its sealed product space.
High-speed metering pump with sealed product space
The high-speed metering pump has been especially developed for metering poorly-lubricating media. “The high-speed pump is particularly advantageous in the chemical industry, which conveys aggressive acids”, reports Thorsten Wagener, the salesman responsible for industrial and chemical application pumps at Oerlikon Barmag.
The main advantage of the pump is the sealed product space. The space that comes into contact with the media is therefore limited to the area around the gears. The external, ball-bearing support points in the high-speed pump are externally lubricated, hence ensuring that the product to be metered does not cause damage as a result of poor lubrication. This extends the lifespan of the pump considerably.
Furthermore, the enlarged speed range (30-500 rpm) permits a large application range for which several pumps of varying sizes have had to be used to date. This cuts back on conversion times, while simultaneously reducing spare parts inventories. With its low weight of 1.4 kg, the compact pump (ø65mm) promises both considerable space savings and less wear on the machine.
GM range under the most challenging conditions
The pumps in the GM and GA series provide precision metering with low-pulsation feeding of the conveying medium. The multi-stage GM pump conveys low-viscosity media (i.e., 250 bar, 100 mPas) even under high pressure and in the most challenging conditions. The square design from the proven GM series is the standard pump for many metering tasks. The development of the multi-stage pump expands the applications range for the GM series considerably. The round 2-stage GM pump has been developed especially for use in high-pressure technology. It masters the particular challenge of conveying small throughputs with low viscosities. The pump is perfect for 0.05 through 20 cm³/rev feed sizes and is excellently suited for use in high-pressure machines for PUR molded parts, foam slab stock, refrigeration unit insulations and sandwich panels, for example.
GA series pumps for high-viscosity media
Manufacturing companies are constantly facing the challenge of making their products and processes more efficient. Oerlikon Barmag has supplemented the tried-and-tested GM range with the GA series, developed especially for the challenging conveying of high-viscosity media. The GA series pumps are available for conveying volumes of between 1.25 and 30 cm³/rev (0.6-144 l/h). They have been designed for pressures of up to 200 bar, for viscosities of up to 1,500 Pas as well as for temperatures of up to max. 225 °C. With this range of pumps, Oerlikon Barmag offers its customers tailor-made solutions for many technical processes in which high-precision and even metering is of paramount importance.
The drum pump – conveying and metering using a single unit
With the drum pump, the Oerlikon Barmag pump specialists have created a pump designed specifically for conveying and metering high-viscosity materials such as adhesives, silicones and other high-viscosity materials from drums and other large containers and for pressures of up to 250 bar. Its special features not only include the fact that it removes high-viscosity materials from the drum, but that it also meters the medium directly without any additional interim stops.
Gear pump and drum follower plate are aligned to each other so that the plate can effortlessly reach the bottom of the container, hence leaving a very low residue of <1%. “This has a positive impact on both the material costs and the production process”, sums up Thorsten Wagener. The metering, which to date has been carried out in two steps requiring scoop-piston and metering pumps, can now be merged in into a single unit with the drum pump.
About Oerlikon
Oerlikon (SIX: OERL) is a global innovation powerhouse for surface engineering, polymer processing and additive manufacturing. Its solutions and comprehensive services, together with its advanced materials, improve and maximize the performance, function, design and sustainability of its customers’ products and manufacturing processes in key industries. Pioneering technology for decades, everything the company invents and does is guided by its passion to support its customers’ goals and foster a sustainable world. Headquartered in Pfäffikon, Switzerland, the Group operates its business in two divisions – Surface Solutions and Polymer Processing Solutions. It has a global footprint of more than 10,600 employees at 179 locations in 37 countries and generated sales of CHF 2.3 billion in 2020.
For more information: www.oerlikon.com
About the Oerlikon Polymer Processing Solutions division
With its Oerlikon Barmag, Oerlikon Neumag, Oerlikon Nonwoven and Oerlikon HRSflow brands, the Oerlikon Polymer Processing Solutions Division is focusing on manmade fibers plant engineering and flow control equipment solutions. Oerlikon is one of the leading providers of manmade fiber filament spinning systems, texturing machines, BCF systems, staple fiber systems and solutions for the production of nonwovens and – as a service provider – offers engineering solutions for the entire textile value added chain. Furthermore, Oerlikon has a high precision flow control components business that offers a large selection of gear metering pumps for the textile and other industries, including the automotive, chemical and paint markets. With Oerlikon HRSflow the division develops innovative hot runner systems for the polymer processing industry. In cooperation with Oerlikon Balzers, highly-efficient and effective coating solutions are offered here from a single source.
As a future-oriented company, the research and development at this division of the Oerlikon Group is driven by energy efficiency and sustainable technologies (e-save). With its range of polycondensation and extrusion systems and their key components, the company caters to the entire manufacturing process – from the monomer all the way through to the textured yarn and other innovative polymer processed materials and applications. The product portfolio is rounded off with automation and Industrie 4.0 solutions.
The primary markets for the product portfolio of Oerlikon Barmag are in Asia, especially in China, India and Turkey, and – for those of Oerlikon Neumag and Oerlikon Nonwoven – in the USA, Asia, Turkey and Europe. Oerlikon HRSflow is particularly at home in the core automotive markets. These include Germany, China, Korea and Brazil. Worldwide, the division – with more than 4,500 employees – has a presence in 120 countries with production, sales and distribution and service organizations. At the Research and Development centers in Remscheid, Neumünster (Germany), San Polo di Piave, Treviso (Italy) and Suzhou (China), highly-qualified engineers, technologists and technicians develop innovative and technologically leading products for tomorrow’s world.
For more information: www.oerlikon.com/polymer-processing