hycuTEC sets new standards in terms of quality and efficiency
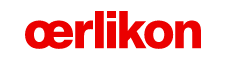
Neumünster, March 10, 2022 – the Neumünster-based systems builder Oerlikon Nonwoven premiered its new hycuTEC hydro-charging solution at this year’s FILTECH in Cologne. This new technology for charging von nonwovens enables the filter efficiency to be increased to more than 99.99%. As a result, it offers meltblown producers considerable material savings with simultaneously improved filtration.
The hycuTEC is the market’s first industrially-manufactured hydro-charging solution that can also be seamlessly integrated into the production process. And the innovative technology is also easily retrofitted to existing systems as a plug & produce component – a first within the market.
Filter media with a whole new level of quality
hycuTEC hydro-charging can reduce the pressure loss in typical FFP2 filter media to less than a quarter. Even filtration efficiencies of more than 99.99% are easily achieved in typical filter media of 35 g/m² at 35 Pa. Tests at pilot customers manufacturing FFP2 face masks have confirmed quality increases due to the improved filtration with a simultaneous reduction in material usage of 30%. For end users, the consequence is noticeably improved comfort resulting from significantly reduced breathing resistance.
In addition to this, the hydro-charging unit also stands out in terms of sustainability: “The hycuTEC process excels as a future-proof technology due to its considerably lower water and energy con-sumption compared to other hydro-charging concepts. This unit allows an additional drying process to be dispensed with in many applications, which has a huge impact on energy consumption”, comments Dr. Ingo Mählmann, Head of Sales & Marketing at Oerlikon Nonwoven. Incidentally, the hycuTEC unit can be easily and quickly installed and is simple to operate, set and service, while also being extremely user-friendly.
Technological quantum leap
Whereas classical hydro-charging processes charge the finished non-woven material, the hycuTEC concept is based on the all-round charging of each filament. Through controlled atomization, a charge is evenly transferred to the fibers from the water spray. And a special additive is used to permanently bond the charge to the surface of each fiber. The result: filter media with a uniformly stable charge over the entire cross-section and an effective fiber surface area about 10 times greater than that of surface-charged media. Integrating the new unit into a state-of-the-art Oerlikon Nonwoven meltblown system helps achieve a uniformly high product quality across the whole production process.
About Oerlikon
Oerlikon (SIX: OERL) is a global innovation powerhouse for surface engineering, polymer processing and additive manufacturing. Its solutions and comprehensive services, together with its advanced materials, improve and optimize the performance, function, design and sustainability of its customers’ products and manufacturing processes in key industries. Oerlikon has been a technology pioneer for decades. All developments and activities have their origins in the passion for supporting customers in achieving their objectives and increasing sustainability. Headquartered in Pfäffikon, Switzerland, the group has two divisions: Surface Solutions and Polymer Processing Solutions. The group has a global footprint of more than 11,800 employees at 207 locations in 38 countries and generated sales of CHF 2.65 billion in 2021.
For further information: www.oerlikon.com
About the Oerlikon Polymer Processing Solutions division
With its Oerlikon Barmag, Oerlikon Neumag, Oerlikon Nonwoven and Oerlikon HRSflow brands, the Oerlikon Polymer Processing Solutions Division is focusing on manmade fibers plant engineering and flow control equipment solutions. Oerlikon is one of the leading providers of manmade fiber filament spinning systems, texturing machines, BCF systems, staple fiber systems and solutions for the production of nonwovens and – as a service provider – offers engineering solutions for the entire textile value added chain. Furthermore, Oerlikon has a high precision flow control components business that offers a large selection of gear metering pumps for the textile and other industries, including the automotive, chemical and paint markets. With Oerlikon HRSflow the division develops innovative hot runner systems for the polymer processing industry. In cooperation with Oerlikon Balzers, highly-efficient and effective coating solutions are offered here from a single source.
As a future-oriented company, the research and development at this division of the Oerlikon Group is driven by energy efficiency and sustainable technologies (e-save). With its range of polycondensation and extrusion systems and their key components, the company caters to the entire manufacturing process – from the monomer all the way through to the textured yarn and other innovative polymer processed materials and applications. The product portfolio is rounded off with automation and Industrie 4.0 solutions.
The primary markets for the product portfolio of Oerlikon Barmag are in Asia, especially in China, India and Turkey, and – for those of Oerlikon Neumag and Oerlikon Nonwoven – in the USA, Asia, Turkey and Europe. Oerlikon HRSflow is particularly at home in the core automotive markets. These include Germany, China, Korea and Brazil. Worldwide, the division – with more than 4,500 employees – has a presence in 120 countries with production, sales and distribution and service organizations. At the Research and Development centers in Remscheid, Neumünster (Germany), San Polo di Piave, Treviso (Italy) and Suzhou (China), highly-qualified engineers, technologists and technicians develop innovative and technologically leading products for tomorrow’s world.
For further information: www.oerlikon.com/polymer-processing