Sustainable solutions for the entire process chain
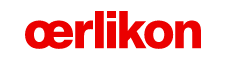
Remscheid/Düsseldorf, October 13, 2022 – The Swiss Oerlikon Group’s Polymer Processing Solutions division will be presenting itself at the K 2022 under the banner of ‘Feel the Flow. Keep Control’. The leading international trade fair for the plastics industry is taking place in Düsseldorf, Germany, between October 19 and 26 this year, with around 200,000 visitors expected. Oerlikon will be presenting a broad range of products and services focused on manufacturing and processing plastics. Innovative solutions and technologies concentrating on such topics as raw material preparation based on modern polycondensation and extrusion systems, the latest recycling technologies, efficient hot runner systems, innovative coating solutions, sustainable manufacturing processes for filtration applications and high-quality gear metering pumps. Oerlikon’s team of experts is very much looking forward to seeing you at Stand D10 in Hall 1.
Today, innovation no longer means producing ever faster and ever more, but also producing sustainably. The plastics industry is as aware of its responsibility with regards to sustainability as it is of the demands that end users and politicians place on their products. Correspondingly, the focus of the eight K 2022 trade fair days will be on topics such as reducing CO2 emissions, avoiding waste, energy efficiency and the continual expansion of the circular economy.
Climate neutrality, circular economy and digitalization – the focal topics of the K 2022
“We see our technology solutions as enablers of a better world”, states Georg Stausberg, CEO of the Oerlikon Polymer Processing Solutions division and CSO of the Oerlikon Group. “In the polymer processing industry, we have to come to a sustainable, closed circular economy for packaging materials and textiles, for example, while simultaneously intensively expanding the recycling of the materials used. With our current technologies and our future innovations, we support manufacturers along the entire process chain in achieving their own sustainability targets.”
With its technology brands and subsidiaries, the Swiss Oerlikon Group is a solutions provider for numerous applications and stages within the plastics industry. Oerlikon will be showcasing a broad portfolio of innovative products and services at the K 2022 in Düsseldorf.
From polycondensation, extrusion and pumps all the way through to hot runner systems
High-quality melt has a direct impact on the end product. It forms the basis for high-end bottle, film and fiber polyester. The efficient, high-quality Oerlikon Barmag Huitong Engineering continuous polycondensation systems produce homogeneous melt by means of a chemical reaction during which different monomers are joined together to create polymers. The benefits of having your own polycondensation system: non-reliance on external granulate manufacturers, offsetting of short-term raw material market price fluctuations and direct influence on the polymer quality. Topics that the Oerlikon polymer experts would like to discuss in person with visitors at the K 2022. These also include the new application possibilities for processing new, sustainable materials.
Stable manufacturing processes and less waste
“Longer service lives for components and tools increase efficiency in plastics-processing manufacturing. But they also provide for more stable processes and hence less waste”, explains André Wissenberg, Head of Marketing, Corporate Communications and Public Affairs at the Oerlikon Polymer Processing Solutions division. “And all our technology brands and the innovations being presented at the K 2022 have a clear focus on this these”.
Numerous exhibits and virtual experiences
On the occasion of the K 2022, Oerlikon Barmag will be showcasing exhibits including eccentric screw pumps for conveying highly-filled, high-viscosity and abrasive media. Furthermore, there will also be a spotlight on a new pump for conveying high-viscosity, shear-sensitive materials such as adhesives and silicones. Using virtual reality glasses, visitors will even be able to delve into the pumps themselves.
Innovative flow control equipment
Hot runner specialist Oerlikon HRSflow will be showcasing a comprehensive hot runner assortment that is tailored to small shot weights as well as its new Xp nozzle series for use in thin-wall injection molding. Both support the trend towards greater sustainability by helping to reduce energy and material consumption in plastics processing. Oerlikon FLEXflow hot runner technology applications and other progressive hot runner solutions specially developed for PCR materials and biopolymers will also be presented at the stands of several partner companies (see below).
Coating solutions for plastic components and tools
A further Oerlikon Surface Solutions division technology brand will also be attending the K 2022, with Oerlikon Balzers presenting BALINIT MOLDENA, a new coating for the injection molding process, and the extrusion of filled polymers with outstanding abrasion and corrosion resistance. This coating is the optimum solution for processing new and recyclable plastics, for improving energy efficiency and for reducing the consumption of resources. A current application is the fully-electric BMW iXe SUV, which utilizes ePD™ technology (embedded PVD for Design parts) from Oerlikon Balzers – a future-oriented, environmentally-friendly coating process for high-quality, metallic-looking surfaces on plastic parts with intelligent functionalities. Here, Oerlikon Balzers will also be providing information on INUBIA I (Integrated) – the fully-integrated, automated solution for large-scale plastic metallization. The INUBIA I 6 and I 15 are fully-automated, user-friendly systems for applying ePD™-based coatings. The integrated systems, developed in their entirety by Oerlikon Balzers, permit high-volume mass production as demanded by the automobile industry.
Technologies for manufacturing nonwovens and sustainable filtration applications
The Oerlikon Nonwoven meltblown process can be used to manufacture nonwovens made from classical virgin elastomer-based and bio-based raw materials, including PLA and TPU products with recycled content. With its hycuTEC hydro-charging solution, Oerlikon Nonwoven will also be presenting its new technology for charging nonwovens, which increases filter efficiency to more than 99.99% with simultaneous material savings of up to 30%. hycuTEC enables considerably lower water and energy consumption, as this system allows an additional drying process to be dispensed with in the case of many applications.
State-of-the-art systems for recycling plastics
Oerlikon’s joint venture company BBEngineering has been looking at the topic of recycling for many years now and has made it the focus of its presence at the Düsseldorf trade fair this year. In addition to extruders, filters and mixers, BBEngineering offers the VacuFil® – a complete system that enables innovative, unique PET LSP recycling. VacuFil® unites gentle large-scale filtration and targeted IV regulation for consistently-excellent rPET melt quality. The modular system can be used for various recycling applications.
Diverse accompanying program: presentation series and open-house event
In addition to product and technology innovations, Oerlikon will be offering a diverse accompanying program at the K 2022:
- Visitors to the stand will be shown the company’s total solutions offering in an audiovisual 4D experience: in a 15-minute simulator flight, attendees – by invitation – will be taken on an exciting journey into the future of a sustainable circular economy with technology solutions from the Oerlikon Group.
- Thanks to the trade fair’s close proximity to the Oerlikon Barmag site in Remscheid, existing and potential customers will also be offered an insight into the world’s largest manmade fiber R&D Center. They can watch how PET waste is processed into high-quality recycled yarn at the BBEngineering Recycling Technology Center. There will be an open-house event running parallel to the trade fair over four days (October 20, 21, 24 and 25, 2022), which will be by invitation only.
- And there will be numerous presentations on current topics taking place daily at the Oerlikon trade fair stand D10 in Hall 1: these include a report from Oerlikon HRSflow, ENGEL and Borealis on a joint project for a digital process twin project. The current program can be seen in Düsseldorf and online: https://www.oerlikon.com/polymer-processing/en/#!/clp/polymer-processing/en/custom-landing-pages/sustainable-solutions-along-the-value-chain/.
- Furthermore, Oerlikon technology will also be showcased at the stands of numerous partners throughout the trade fairs grounds:
o ENGEL (Hall 15, Stand C58, door cladding and smart back panel)
o Tederic (Hall 15, Stand D40, 2K high-gloss B pillar)
o Arburg (Hall 13 / Stand A13-B13, multi-component tool box made from PC+ABS and RECOPOUND® – the PET-based recycled
material from Leonard Kurz)
o Haitian (Hall 15, Stand A57, fruit crate made from PE plus Tetra Pak recycled shredded flakes)
o Wittmann-Battenfeld (Hall 15, Stand C06, 3K coffee cups)
o Billion (Hall 15, Stand B24, gardening tools)
o Netstal (Hall 15, Stand D24, thin-wall R-PP cups).
Visiting the K 2022, and the Oerlikon trade fair stand D10 in Hall 1 in particular, is well worthwhile.
About Oerlikon
Oerlikon (SIX: OERL) is a global innovation powerhouse for surface engineering, polymer processing and additive manufacturing. The Group’s solutions and comprehensive services, together with its advanced materials, improve and maximize the performance, function, design and sustainability of its customers’ products and manufacturing processes in key industries. Pioneering technology for decades, everything Oerlikon invents and does is guided by its passion to support customers’ goals and foster a sustainable world. Headquartered in Pfäffikon, Switzerland, the Group operates its business in two Divisions – Surface Solutions and Polymer Processing Solutions. It has a global footprint of more than 12 000 employees at 202 locations in 37 countries and generated sales of CHF 2.65 billion in 2021.
For further information: www.oerlikon.com
About the Oerlikon Polymer Processing Solutions division
With its Oerlikon Barmag, Oerlikon Neumag, Oerlikon Nonwoven and Oerlikon HRSflow brands, the Oerlikon Polymer Processing division focuses on manmade fibers plant engineering and flow control equipment solutions. Oerlikon is one of the leading providers of manmade fiber filament spinning systems, texturing machines, BCF systems, staple fiber systems and solutions for the production of nonwovens and – as a service provider – offers engineering solutions for the entire textile value added chain. Furthermore, Oerlikon offers a range of a high-precision flow control solutions. This currently includes a large selection of gear metering pumps for the textile and other sectors such as automobile construction, the chemical industry and the dyes and lacquers industry. With Oerlikon HRSflow, the division develops innovative hot runner systems for the polymer processing industry. In collaboration with Oerlikon Balzers, it offers highly-efficient, effective coating solutions from a single source.
As a future-oriented company, the research and development at this division of the Oerlikon Group is driven by energy efficiency and sustainable technologies (e-save). With its range of polycondensation and extrusion systems and their key components, the company caters to the entire manufacturing process – from the monomer all the way through to the textured yarn and other innovative polymer materials and applications. The product portfolio is rounded off with automation and Industrie 4.0 solutions.
The primary markets for the product portfolio of Oerlikon Barmag are in Asia, especially in China, India and Turkey, and – for those of Oerlikon Neumag and Oerlikon Nonwoven – in the USA, Asia, Turkey and Europe. Oerlikon HRSflow is, above all, active in the key automotive markets. These include Germany, China, Korea and Brazil. Worldwide, the division – with more than 4,500 employees – has a presence in 120 countries with production, sales and distribution and service organizations. At the research and development centers in Remscheid, Neumünster (both Germany), San Polo di Piave / Treviso (Italy) and Suzhou (China), highly-qualified engineers, technologists and technicians develop innovative and technologically-leading products for tomorrow’s world.
For further information: www.oerlikon.com/polymer-processing